There are metal materials commonly used by processing manufacturers to deal with. This time I will share 24 commonly used materials for machinery and mold processing. The materials are all understood, and it is easier to match the knife.
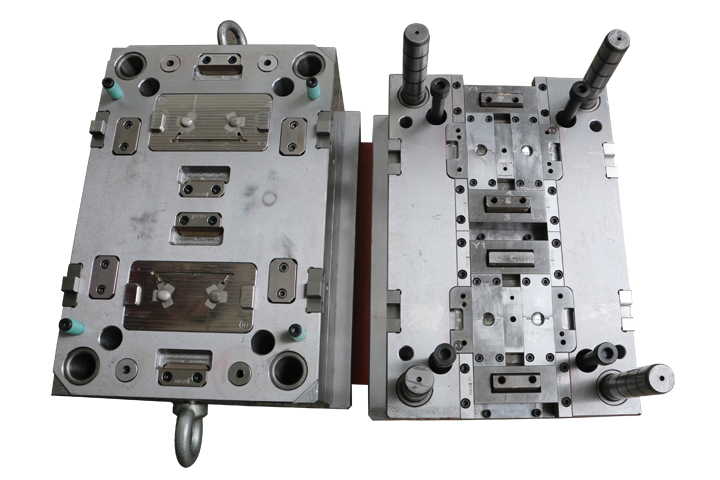
1, 45-high-quality carbon structural steel, is the most commonly used medium-tempered and tempered steel
Main features: The most commonly used medium carbon quenched and tempered steel has good comprehensive mechanical properties, low hardenability, and cracks easily during water quenching. Small parts should be quenched and tempered, and large parts should be normalized. Application examples: Mainly used for manufacturing high-strength moving parts, such as turbine impellers and compressor pistons. Shafts, gears, racks, worms, etc. Welding parts should be preheated before welding and stress relief annealing after welding.
2. Q235A (A3 steel)-the most commonly used carbon structural steel
Main features: High plasticity, toughness and welding performance, cold stamping performance, as well as certain strength and good cold bending performance. Application examples: Widely used for parts and welding structures with general requirements. Such as low tension rods, connecting rods, pins, shafts, screws, nuts, ferrules, brackets, bases, building structures, bridges, etc.
3. 40Cr-one of the most widely used steel types, which is an alloy structural steel
Main features: After quenching and tempering, it has good comprehensive mechanical properties, low temperature impact toughness and low notch sensitivity, good hardenability, high fatigue strength when oil-cooled, and parts with complex shapes when water-cooled. Generate cracks, moderate cold bend plasticity, good machinability after tempering or tempering, but poor weldability, easy to crack, preheat to 100 ~ 150 ℃ before welding. Generally, it can be used in the quenched and tempered state. Carburizing and high frequency surface hardening. Application example: After quenching and tempering, it is used to manufacture medium-speed and medium-load parts, such as machine tool gears, shafts, worms, spline shafts, thimble sleeves, etc., after quenching and tempering and high-frequency surface hardening, it is used to produce high-hardness and resistance to surface. Grinding parts, such as gears, shafts, main shafts, crankshafts, mandrels, sleeves, pins, connecting rods, screws and nuts, intake valves, etc., are used to produce heavy-duty, medium-speed impact after quenching and tempering at moderate temperatures Parts, such as oil pump rotors, sliders, gears, main shafts, collars, etc., are used to manufacture heavy-duty, low-impact, wear-resistant parts such as worms, spindles, shafts, collars, etc. after quenching and low temperature tempering. Carbon After the nitriding, the transmission parts, such as shafts and gears, with larger size and higher low temperature impact toughness are manufactured later.
4, HT150-gray cast iron
Application examples: gear box, machine bed, box, hydraulic cylinder, pump body, valve body, flywheel, cylinder head, pulley, bearing cover, etc.
5, 35-common materials for various standard parts and fasteners
Main features: Appropriate strength, good plasticity, high cold plasticity, and good weldability. It can be partially upset and brushed in cold state. Low hardenability, use after normalizing or quenching and tempering Application examples: Suitable for manufacturing small cross-section parts, parts that can withstand large loads: such as crankshafts, levers, connecting rods, shackles, etc., various standard parts, fasteners .
6, 65Mn-commonly used spring steel
Application examples: small flat and round springs, cushion springs, springs, spring rings, valve springs, clutch springs, brake springs, cold-rolled coil springs, snap springs, etc.
7, 0Cr18Ni9-the most commonly used stainless steel (US steel number 304, Japanese steel number SUS304)
Characteristics and applications: It is the most widely used as stainless heat-resistant steel, such as food equipment, general chemical equipment, and original industrial equipment.
8. Cr12——Commonly used cold work die steel (American steel grade D3, Japanese steel grade SKD1)
Features and applications: Cr12 steel is a widely used cold work die steel, which is a high carbon and high chromium type bainite steel. The steel has good hardenability and good wear resistance. Because the carbon content of Cr12 steel is as high as 2.3%, the impact toughness is poor, it is easy to brittle, and it is easy to form non-uniform eutectic carbide. It has good abrasion resistance, and is mostly used to manufacture cold punches, punches, blanking dies, cold heading dies, cold extrusion dies and cold dies, drill sleeves, and gauges that require high wear resistance with less impact load , Drawing die, embossing die, wire drawing board, drawing die and cold pressing die for powder metallurgy.
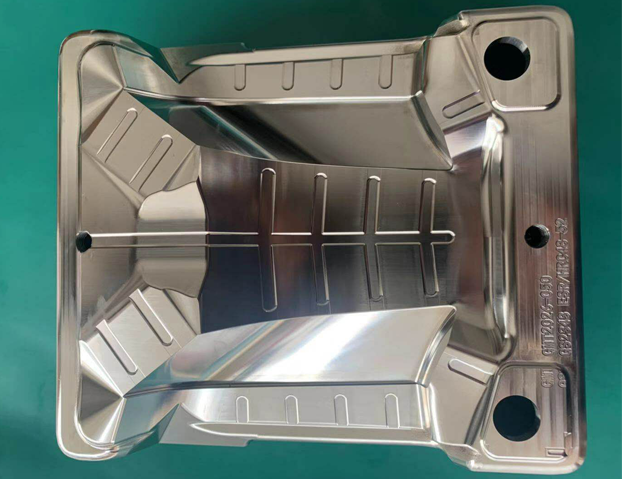
9, DC53-commonly used cold-work die steel imported from Japan
Features and applications: High-strength and toughness cold-working die steel, Japan Datong Special Steel Co., Ltd. steel grade. After high temperature tempering, it has high hardness, high toughness, and good wire cutting. Used for precision cold stamping die, drawing die, wire rolling die, cold punching die, punch, etc. 10, SM45-ordinary carbon plastic mold steel (Japanese steel number S45C)
10.DCCr12MoV-wear-resistant chrome steel
Made in China. Compared with Cr12 steel, the carbon content is lower, and Mo and V are added. The carbide unevenness is improved. MO can reduce carbide segregation and improve hardenability. V can refine grains and increase toughness. This steel has high Hardenability, cross-section below 400mm can be fully hardened, good hardness and wear resistance can be maintained at 300 ~ 400 ℃, higher toughness than Cr12, small volume change during quenching, and high wear resistance and Good comprehensive mechanical properties. So it can manufacture various molds with large cross-sections, complex shapes, and withstanding large impacts, such as ordinary drawing dies, punching concave dies, punching dies, blanking dies, cutting dies, piping dies, wire drawing dies , Cold extrusion die, cold cutting scissors, circular saw, standard tools, measuring tools, etc.
11.SKD11-ductile chrome steel
Japan Hitachi production. Technically improve the cast structure in steel and refine the grains. Compared with Cr12mov, the toughness and wear resistance have been improved. The service life of the mold has been extended.
12, D2-high carbon high chromium cold work steel
Made in the United States. It has high hardenability, hardenability, wear resistance, high temperature oxidation resistance, good rust resistance after quenching and polishing, and small heat treatment deformation. It is suitable to manufacture various cold work molds that require high precision and long life. Tools and measuring tools, such as tensile die, cold extrusion die, cold shear knife, etc.
13.SKD11 (SLD)-non-deformable and tough high chromium steel
Japan Hitachi production. As the content of MO and V in steel increases, the cast structure in steel is improved, the grains are refined, and the morphology of carbides is improved, so the steel's strong toughness (bend strength, deflection, impact toughness) Etc.) Higher than SKD1, D2, wear resistance has also increased, and has higher tempering resistance. Practice has proven that the life of this steel mold has been improved compared to Cr12mov. Often manufacturing molds with high requirements, such as tensile molds, impact Moulds for grinding wheels.
14, DC53-high toughness and high chromium steel
Japan Datong production. Heat treatment hardness is higher than SKD11. After high temperature (520-530) tempering, it can reach 62-63HRC high hardness, DC53 exceeds SKD11 in strength and wear resistance. Toughness is twice as high as SKD11. There are few cracks and cracks in cold work mold manufacturing. It greatly improves the service life. The residual stress is small. The residual stress is reduced by turning back at high temperature. Because the cracks and deformation after wire cutting are suppressed. The machinability and abrasiveness exceed SKD11. For precision stamping dies, cold forging, deep drawing dies, etc.
15.SKH-9-general high-speed steel with high wear resistance and toughness
Japan Hitachi production. Used for cold forging die, slitting machine, drill, reamer, punch, etc.
16.ASP-23——Powder Metallurgy High Speed Steel
Made in Sweden. Extremely uniform carbide distribution, wear resistance, high toughness, easy processing, stable heat treatment size. Used for various long-life cutting tools such as punches, deep drawing dies, drilling dies, milling cutters and shear blades .
17.P20——Generally required size plastic mold
Produced in the United States. Corrosive operation. Pre-hardened HB270-300. Hardened hardness HRC52.
18, 718-high-demand size plastic mold
Made in Sweden. Especially for electro-erosion operation. Pre-hardened HB290-330 in factory state. Hardened hardness HRC52
19.Nak80-high mirror, high precision plastic mold
Produced by Datong in Japan. Pre-hardened HB370-400. Hardened hardness HRC52
20, S136-anti-corrosion and mirror-polished plastic mold
Made in Sweden. Pre-hardened HB <215. Hardened hardness HRC52.
21, H13-common commonly used die casting mold
For aluminum, zinc, magnesium and alloy die casting. Hot stamping die, aluminum extrusion die,
22.SKD61-advanced die casting mold
Produced by Hitachi, Japan, the electro-hydraulic remelting technology has a significant improvement in service life over H13. Hot stamping die, aluminum extrusion die,
23, 8407-advanced die casting mold
Made in Sweden. Hot stamping die, aluminum extrusion die.
24.FDAC-Added sulfur to enhance its machinability
The factory pre-hardened hardness is 338-42HRC, which can be directly engraved without quenching and tempering. It is used for small batch molds, simple molds, various resin products, sliding parts, mold parts with short lead times. Zipper molds, Glasses frame mould