Consumer electronics products refer to audio and video products for personal and home-related radio and television, and electronics molds include TV molds, DVD player (VCD, SVCD, DVD) molds, video recorder molds, camcorder molds, radio molds, Recorder mold, in some developed countries, telephones, personal computers, home office equipment, home electronics medical equipment and automotive electronics are also included in consumer electronics. With the development of technology and the emergence of new products and applications, digital cameras, mobile phones, PDAs and other products have also become emerging consumer CNC electronic products.
The metal structural components of consumer electronics products refer to the protection and support of high dimensional accuracy, high surface quality stars and high-performance hardware components in consumer electronics products. A wide range of products is an important part of consumer electronics. Metal structural components of consumer electronics are important components of consumer electronics. Their design and manufacturing account for about half of the mobile consumer electronics product development cycle, and their cost accounts for about 15% of the cost of mobile consumer electronics materials.
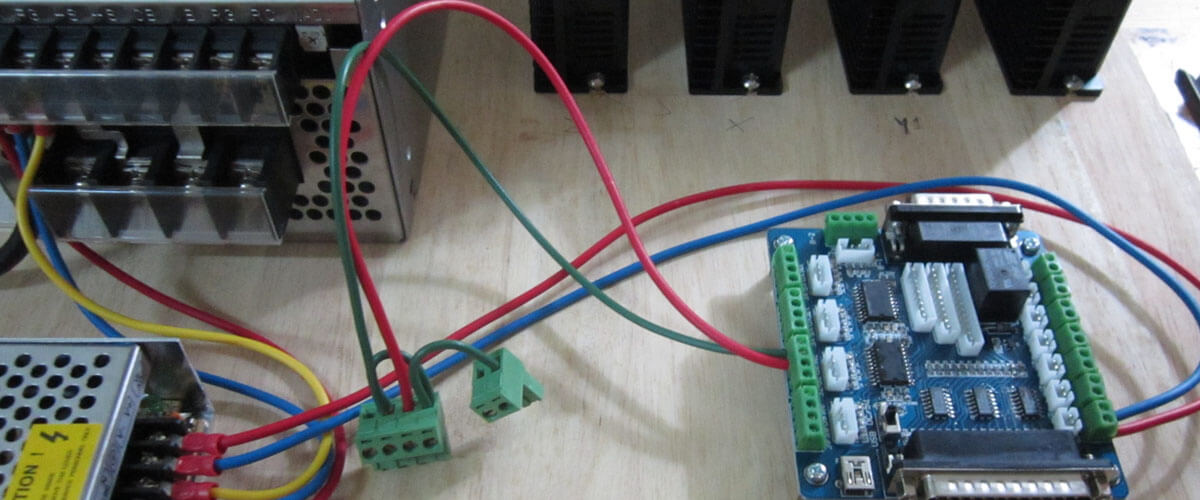
According to the raw materials, the structural part molds of consumer electronics are mainly divided into ABS engineering plastic part molds, polycarbonate part molds, metal part molds, etc. Among them, metal parts mainly include magnesium alloy part molds and stainless steel part molds. Steel parts. For a long time, ABS engineering plastics are the main materials for structural components of consumer electronics, but plastic structural components usually have the disadvantage of poor durability. Metal structural parts are fascinated by consumers for their thin materials, high-strength support, good texture, and fast heat dissipation. In the past two years, it has been increasingly used in high-end products by consumer electronics manufacturers.
Consumer CNC Electronic Development
With the development of thin and light consumer electronics, stylish and distinctive components. Metal structural parts have the advantages of high strength, good toughness, fast heat dissipation, lightweight and good texture, etc., and have obtained obvious advantages in the market. Mainstream development trends. With the development of new processing technologies, processes and consumer acceptance, the application of new material structural components will also occupy a place in the future.
The rapid development of the global consumer electronics market has provided a broad market space for the development of the metal structure mold industry for consumer electronics products, and the industry has expanded rapidly. At the same time, the trend of diversification, personalization, and thin and light appearance of smart terminals for consumer electronics products, as well as the structural complexity caused by the rise of wearable devices, has continued to improve the technological level, innovation ability and production process of smartphones. Metal structure mold industry. Consumer electronics products' demand for metal structural parts molds is growing rapidly.
Consumer CNC Electronic Products Rapid Development
With the improvement of people's consumption level, the demand for consumer CNC electronic products is expanding, product upgrades are accelerating, the scale of the consumer electronics market is constantly growing, and the mold-related industries are also rapidly developing. Data show that driven by the rapid growth of smartphones, tablets, PCs and other terminal devices, the global consumer electronics market reached nearly 790 billion euros in 2015, an increase of 15% over the previous year.
The scale of China's electronic information industry has continued to expand, and a relatively complete manufacturing system and industrial supporting infrastructure have been formed. According to the National Bureau of Statistics, China's electronics and information industry sales revenue reached 15.4 trillion yuan in 2015, an increase of more than 10.4%. China's electronic information manufacturing industry above designated size achieved a sales output value of 113,294.60 billion yuan, an increase of 9.0%. The output value of major products such as mobile phones and integrated circuits reached 1.81 billion and 108.72 billion, respectively, a year-on-year increase of 7.8% and 7.1%. The output of consumer electronics products such as mobile phones, personal computers, and tablet computers accounted for more than 50% of global output, ranking first in the world.
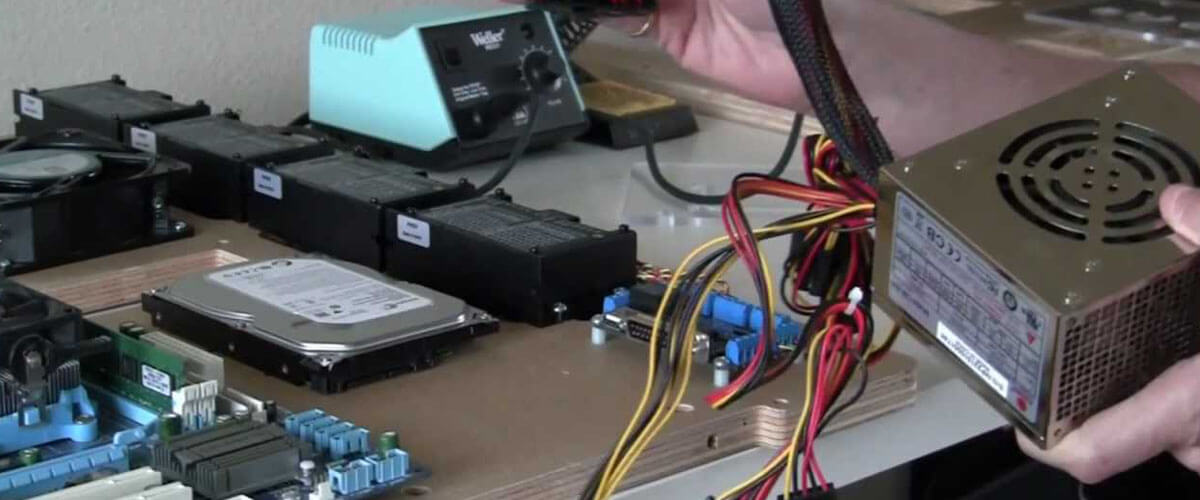
Tips on two shot peening die
Multi-color multi-material injection molding refers to combining several plastics into one multi-functional part in one manufacturing process or one production unit. This technology uses multiple materials for injection molding and combines the characteristics of different materials during assembly or other suitable bonding methods to improve the functionality and aesthetics of the product, significantly save costs and provide new designs possibility.
Necessary conditions for two-color injection
The mating material used for two-color injection molding must meet two basic compatibility conditions, namely adhesive compatibility and process compatibility.
Two-color injection molding also sets new requirements for injection molding equipment. For the injection unit, parallel, horizontal and vertical L-shaped and Y-shaped single-cylinder injection structures can be used. For mixing nozzles, special nozzles such as patterns, waves, flow marks, gradients, and intermediate layers can be selected. In terms of clamping, you can choose the standard type, vertical rotation type, horizontal rotation type, rotation axis type, robot rotation type. In terms of feed, in addition to standard hydraulic motor drives, ESD (electric screw drive) charging structures can also be used. For oil circuits, high-speed injection and closed-circuit designs of ACC accumulators are available.
One of the key factors for two-color injection is the variability of computer-controlled programs. Because even for the same type of multi-color product, if you use different mold designs, you must match different electronic control programs. After purchasing a multi-color injection molding machine, if you encounter a new mold design, an excellent multi-color injection molding machine supplier can quickly upgrade existing equipment to meet injection requirements.
New developments in technology
Combined with the observation of two-color injection molding in recent years, in addition to traditional multi-color products (such as automotive lamp molds, air-conditioning panel molds, and TV frame molds), European and American manufacturers have upgraded to several basic molding technologies. Multicolor injection molding field. "Combination" demos, such as two-color molding and in-mold labeling (IML), two-color molding and in-mold assembly (IMA), two-color molding and stack mold (Stack Mold), two Multi-color moldings plus IML plus IMA plus layer mold can complete two-color molding and sandwich injection on the injection molding machine. Therefore, multi-color injection molding technology has attracted more and more attention, and it can not only present multi-color technology.
Multi-color molding technology for headlights
With the development of the national economy, the automobile industry has become our pillar industry. The rapid development of the current automotive industry has put increasing demands on automotive lighting.
The quality of automotive lighting is very important for driving safety, so regulations in various countries around the world have strict requirements for automotive lighting. The design of luminaires should not only meet regulatory safety requirements but also meet other requirements. For example, the appearance should be integrated with the appearance of the entire vehicle, be beautiful and practical, and meet aerodynamic requirements to make the driver and passengers feel comfortable and convenient. Therefore, with the development of the automotive industry, the design technology of lamps is also changing.
Material and process characteristics of the lamp
The lamp usually consists of a base and a lamp housing. The material of the lamp cap is usually a thermosetting material-BMC (bump molding compound). The lamp shell can be made of PMMA, PP, abs, etc., usually two or three colors. In the production process of two-color lamps, special attention should be paid to the injection port of the two-color injection molding machine. The center distance between the two screws should correspond to the center distance of the two injection molds. There are other important points:
Factors Influencing Lamp Stability
1. Two-color injection control unit response: too many switching points, noise interference, unstable command output, and unstable temperature.
2. The noise of hydraulic system: unstable excitation, valve positioning quality, hysteresis, tubing damping changes.
3. Differences in mechanical systems: internal leaks in oil seals, damping, friction differences, screw check valve positioning, anti-reverse effect
4. Uneven plasticization: differences in plasticized products.
5. Mold temperature control.
Countermeasures for car luminescence
1. Carbonization reduces injection pressure, multi-stage deceleration injection, and mold vacuum.
2. The silver pattern completely dries the plastic particles, increasing the back pressure, reducing the melting temperature, and reducing the rate of fire.
3. Bubbles-increase the backpressure, reduce the melting temperature, use a dehumidifier dryer to increase the size of the gate or runner.
4. Bonding line-increase melt temperature, increase filling speed and increase exhaust and mold temperatures.
5. Gross profit-increase clamping force, reduce filling pressure and lower melting temperature.
6. Shrink uniform thickness design, increase pressure and time, and replace the check valve.
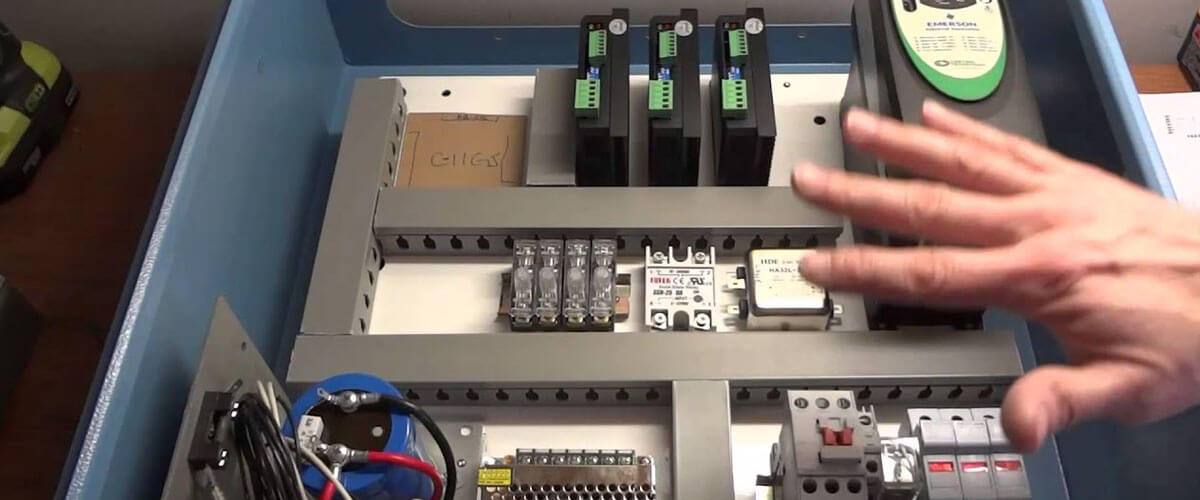
Frequently Asked Questions about Headlamp Plastic Tube Kit Design
1. The screws are not idling.
2. The torque required for the screw is too large to rotate.
3. The plastic is not completely melted.
4. Screw measurement is unstable.
5. Uneven mixing of plastic.
6. Low-temperature plastics tend to rise in temperature.
7. There are air bubbles in the molded product.
8. Molded products are easy to vomit and turn yellow.
9. The screws are prone to corrosion, wear and short life.
Main design points of screw material tube
Plastic screw material tube group is the core component of an injection molding machine, which is responsible for the function of conveying, melting, mixing and metering plastic raw materials. Therefore, the plasticized screw is closely related to the quality of the molded product.
The main purposes of modified plasticized screws are:
1. Improve shear mixing.
2. Stir well.
3. Improve plasticizing ability.
4. Make sure the melt temperature is uniform.
Focus on design screws for taillights
1. L / D ratio: 21-23.
2. The surface roughness of two-color injection molding must be very smooth to avoid accumulation.
3. Improve the corrosion resistance of the coating.
4. Two-color injection compression ratio: 2: 3; feed section: about 50%; compression section: about 30%; metering section: about 20%.
To make a set of two molds, it can be said that the design accounts for 50%. According to industry insiders, the range of requirements for the mold design process is very wide. In addition to requiring the design engineer to have extensive knowledge of mold theory and experience, it is also important to review and think before designing:
Proofreading review-Before completing the design of two injection molds, a proofreading review must be conducted with the customer and related personnel to comprehensively check the overall structure of the drawing structure, processing feasibility and omissions, solicit customer comments and avoid design errors, etc. Molds, used or even scrapped.